INTRODUZIONE
Il
progetto realizzato implementa un sistema di allarme.
La gestione è affidata a:
·
PC
basato su S.O. Windows NT
·
PLC
SAIA PCD1
·
Moduli
R.I.O. ( Remote I/O )
·
Scheda
di comunicazione Applicom
·
PROFIBUS
DP
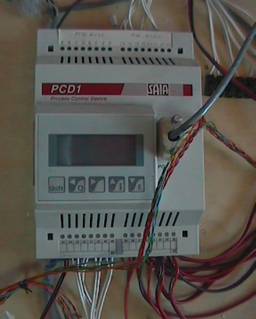
da sinistra: Modulo
RIO e PLC SAIA PCD1
La
realizzazione del progetto si articola in diverse fasi :
1. Costruzione del
plastico;
2. Realizzazione di
un’interfaccia SCADA per il monitoraggio ed il controllo on-line del sistema;
3. Configurazione del
canale di comunicazione tra PC, PLC e moduli RIO;
4. Implementazione di
un programma LADDER per il controllo dei sistemi di sicurezza (sirena,
combinatore telefonico, etc…).
Costruzione del plastico
Il plastico è stato
realizzato in legno compensato e consta di 4 ambienti. Ogni ambiente presenta
finestre e/o porte di cui una a scomparsa come mostrano le foto.
In ogni apertura verso l’esterno (finestra o porta) si è
applicato un Sensore Magnetico:
L’insieme di questi sensori costituiscono l’Allarme
Perimetrale.
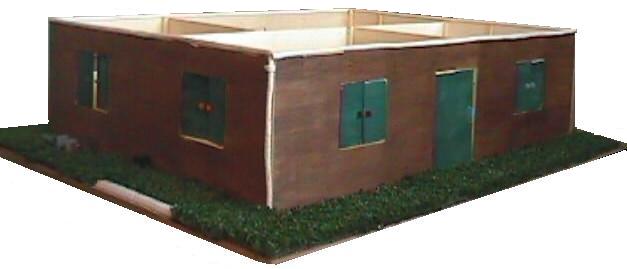
Il Sensore
Magnetico risulta costituito da due magneti permanenti che, se prossimi l’uno
all’altro (condizione di porta o finestra chiusa), realizzano un contatto
normalmente chiuso.
In caso contrario (condizione di porta o finestra aperta),
realizzano un contatto aperto.
Il Sensore
Volumetrico è realizzato attraverso un radar ad infrarosso passivo inserito in
un solo ambiente.
Il radar ad
infrarosso passivo, per il suo funzionamento, necessita di un’alimentazione di
12 ± 15% V DC (da qui
la notazione “passivo”), mentre il suo assorbimento di corrente è di soli 7 mA.
Così come i contatti, anch’esso si comporta come un
interruttore ON-OFF.
La protezione
dell’ambiente avviene mediante la rilevazione di rapidi cambiamenti di livello di
energia infrarossa, presente nell’ambiente, causati da intrusioni.
Il Rilevatore ad
Infrarossi, ha una portata di 12 m ed è provvisto di un Trimmer che permette di
ridurre la portata del 40%.
Tale caratteristica si è rivelata utile viste le ridotte
dimensioni del plastico.
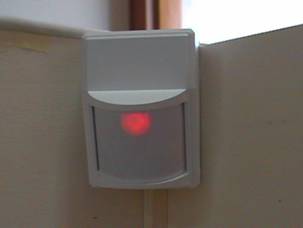
da sinistra: Contatto Magnetico e Sensore Volumetrico
I valori delle
uscite digitali, in campo industriale, sono 0 ¸ 24 V, quindi è stato necessario
l’uso di divisore di tensione, che a fronte di un valore di ingresso di 24 V,
fornisce 2 uscite di 12V.
Ad ogni contatto,
sono stati associati 2 fili con colori univocamente distinguibili (associati
alle maniglie) tranne per il radar, al quale sono stati associati 4 fili, di
cui 2 per l’alimentazione e 2 per il segnale (contatto).
I fili di
collegamento sono stati nascosti nelle pareti del plastico mediante la guaina
di protezione di un cavo coassiale per segnale televisivo.
L’insieme dei fili
è poi stato raccolto in una doppia morsettiera tipo Mammout estraibile per
facilitarne l’interfacciamento verso i moduli di ingresso-uscita.
Il tutto è stato
nascosto con del prato artificiale.
Infine la sirena
d’allarme è stata realizzata con un “Buzzer” ed è attivata direttamente dal PLC
attraverso l’uscita 55.
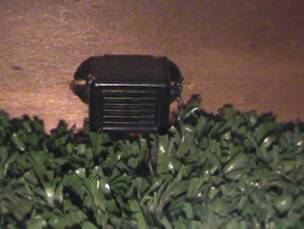
da sinistra: Divisore di Tensione e Buzzer
Realizzazione dell’interfaccia SCADA
Il monitoraggio ed
il controllo on-line dell’intero sistema è stato realizzato utilizzando
l’ambiente di
sviluppo LookOut della National Instruments.
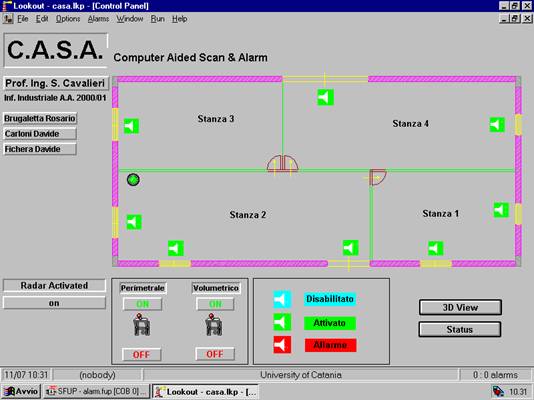
Pannello di
controllo (vista 2D) del sistema di allarme
Si tratta di una
vista planimetrica dello stabile in esame, dove viene evidenziato lo stato
corrente dei sensori di allarme associati ad ogni ambiente.
E’ stato previsto
un doppio comando a seconda del tipo di allarme che l’utente vuole abilitare:
-
Allarme
volumetrico
-
Allarme
perimetrale
Supponendo che
l’utente vada ad abilitare l’allarme volumetrico: in questo caso il nostro
sistema attraversa uno stato transitorio di circa 50 s, tempo necessario per l’inizializzazione
del radar.
E’ possibile avere
una visione tridimensionale del modello o monitorare lo stato di ogni singolo
ambiente, cliccando col mouse sulla zona di interesse.
In questo modo l’utente accederà ad una vista dettagliata
dell’ambiente.
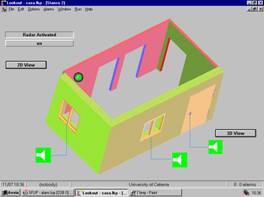
da sinistra: Pannello di controllo (vista 3D)
e vista di un singolo ambiente
Per permettere
all’utente di avere un’analisi storica dello stato del suo sistema, si è
previsto un pulsante STATUS.
In riferimento alla
situazione precedente, premendo il tasto STATUS, viene evidenziata l’ora esatta
in cui è scattato l’allarme. La foto mostra la rappresentazione grafica nel
tempo del valore assunto dall’espressione, in base allo stato dei contatti.
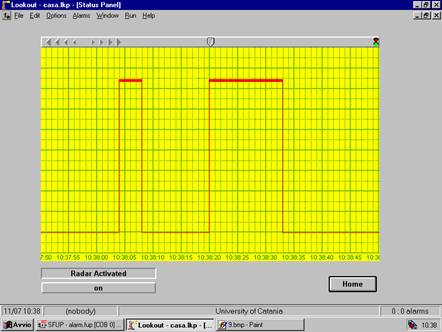
Andamento temporale del segnale “Allarme”
Inoltre è stata
prevista la possibilità di fare tutta una serie di ricerche sull’andamento
temporale degli allarmi.
I collegamenti tra
gli oggetti presenti nel pannello di controllo ed i segnali del nostro sistema
d’allarme sono stati realizzati utilizzando un meccanismo di comunicazione
basato su OPC (Ole for Process Control)
Configurazione del Bus per la comunicazione tra PC e PLC
L’ambiente di
sviluppo della SAIA BURGESS ELECTRONICS, permette di creare una rete di
comunicazione ad hoc tra i device coinvolti nel sistema in esame.
Il progetto consta di 3 file:
-
alarm.fup relativo al programma scritto in
linguaggio LADDER.
-
casa.dp relativo alla configurazione della rete
per la comunicazione tra PC e PLC.
-
init.src necessario per inizializzare la scheda
slave del PLC (XOB 16) e la porta seriale (SASI 9).
La creazione e la
configurazione della rete, per la comunicazione tra PC e PLC, avviene in
maniera grafica. Si definiscono i parametri del sistema: Bus, Master e Slave.
Per il sistema in
esame si è utilizzato:
- un PC
(Master);
- un
PLC (Slave);
- un Profibus-DP.
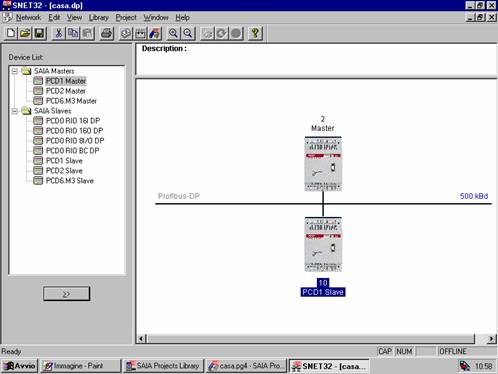
Configurazione
della rete
Nella sottoscheda
“Station”, ogni dispositivo è configurato assegnando l’indirizzo sul bus oltre ad
un nome e al file di programma eseguito (solo nel caso di PLC).
Nella sottoscheda
“Resource” si definiscono gli indirizzi dei Flag di diagnostica per ciascun
dispositivo e il “text name” usato nell’istruzione SASI.
Nella sottoscheda “Modules”,
vengono definiti i moduli per lo scambio di informazioni tra Master/Slave (PC e
PLC).
La presenza di due
moduli di tipo “Master F -> Slave F” è giustificata dalla necessità di
trasferire più di 8 bit (visto che il numero di sensori utilizzato è pari a
9)
Bisogna definire il
Baud rate del BUS.
Per avere accesso
sia in lettura che in scrittura ai dati contenuti nel DATABASE è necessario
andare a definire delle funzioni cicliche di lettura e scrittura. Questo è
possibile usando il programma PCCYC della Applicom.
Scelta la scheda,
bisogna definire le funzioni di interesse che sono 2 nel nostro caso.
In queste funzioni
bisogna definire:
- il
tipo (Read/Write);
-
l’indirizzo del dispositivo da interrogare (10,20,30…);
- il
periodo di refresh;
- il
tipo di variabili di scambio (input packed bit,…);
- il
numero di variabili da scambiare;
-
l’indirizzo sia del DATABASE che del dispositivo in esame, a partire dal quale
sono o devono essere memorizzati i dati scambiati.
Le funzioni appena
definite, sono rese attive dopo aver eseguito l’applicazione Applicom PCInit.
Creazione del programma LADDER per il controllo dei sensori di
allarme
Nel diagramma
Ladder implementato, si sono rappresentati i sensori magnetici con dei contatti
in configurazione OR tra loro e in configurazione AND con il contatto che
rappresenta l’interruttore perimetrale.
Analogamente per il
contatto del radar dove però, per via del ritardo temporale dovuto alla sua inizializzazione,
si è previsto un Function Block di ritardo che abilita il contatto solo dopo
50s dalla chiusura del contatto relativo all’interruttore di alimentazione del
volumetrico.
Si noti che i
contatti utilizzati sono tutti negati poiché i sensori utilizzati sono dei
contatti normalmente chiusi.
Il coil Allarme è
assegnato all’uscita 55 del PLC a cui è connessa la sirena.
La foto seguente
mostra la situazione in cui sia l’allarme perimetrale sia l’allarme volumetrico
sono disabilitati.
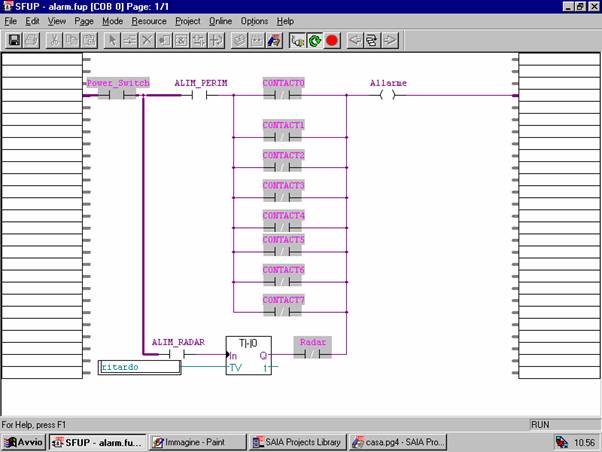
Diagramma Ladder
E’ inoltre presente
il contatto Power_Switch.
Si tratta di un
interruttore di emergenza, in quanto consente di disattivare l’allarme in caso
di avaria del PC o malfunzionamenti dell’interfaccia SCADA.
Tale interruttore è
fisicamente realizzato dall’ingresso 32 del PLC.